
My favorite thing to do growing up was build giant sculptures out of scrap Legos. As I got older I slowly began building more intricate items. This summer, those little Lego pieces turned into giant metal parts as I was introduced to the manufacturing floor of one the most important suppliers to the semiconductor industry in the world, Brooks Automation. I had the privilege to learn more about engineering as a Manufacturing Operations Intern for Richie Mendes at the Brooks campus in Chelmsford.
Brooks Automation is a company that manufactures highly intricate robots that automate the process of making semiconductors. Semiconductor wafers are placed in these robotic machines and the robots modify the wafer to become the semiconductor chips that you see in every electronic device. Brooks’ robots are built in all different shapes and sizes and are customized to each order. Customers then place the robots in a giant building called a “Fab” which runs 24/7.
Brooks’ Manufacturing Operations Team controls and maintains the production and manufacturing of their robots, making sure things run smoothly and on time. The team is responsible for organizing any new projects or restricting the production line. My first task on the team was to reorganize the toolboxes in the cleanroom. I had to first take inventory of all the tools in each toolbox and carefully map out how things should be organized. I worked with the engineers in the room to determine which tools were necessary or unnecessary. I then carefully mapped out a design for a more efficient toolbox layout on each shelf that was specific to the type of robot that they build. From this project, I quickly learned organization is key.
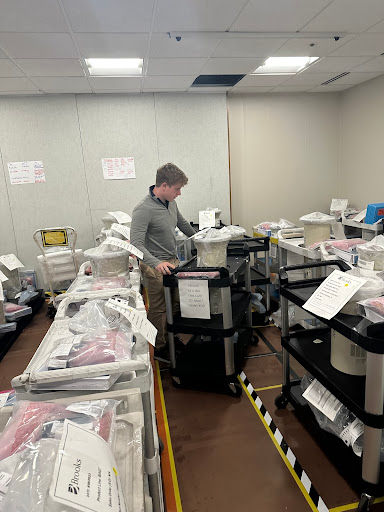
My next responsibility came from joining in on the weekly meeting called the “Gemba walk”. This was a walk to a new lab each week to point out things that needed to be fixed such as safety hazards, unorganized tools or work bays, or too many extra materials. After my first Gemba walk, I was tasked to the Marathon Lab. I had to restructure each work bay to maximize organization and efficiency. I worked alongside a college intern, Ashitesh, to map out a new design. We then took inventory of all the materials needed and showed our plan to the engineers in the lab.

My last task in Manufacturing Operations was to create a floor plan for storing the robots. Robots are shipped from one building in Chelmsford to the other building where they are then taken and put into the machines. There was an overflow of robots and Ashitesh and I needed to find an efficient and uniform way to store them all. It took a lot of tape and a lot of time, but we successfully created a new system in which the engineers could find the robots they needed using the carts and numbers.
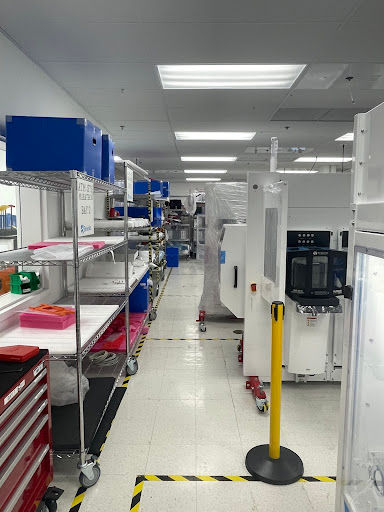
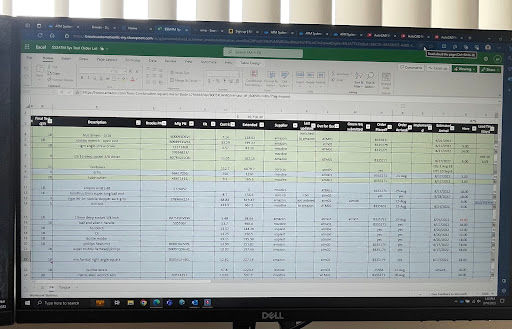
My work at Brooks went beyond just the Manufacturing Operations team. I spent a couple of weeks working for the Electrical Engineering department. I was welcomed by another college intern and I learned a few electrical skills, like how to solder wires, how to tie together wires using a heat gun, and how to sustain electrical current through an electrical box. I also learned a couple of non-electrical skills like drilling holes into the metal electrical box for reliability and testing. I also learned how to plant and maintain tomatoes and cucumbers in the office garden.
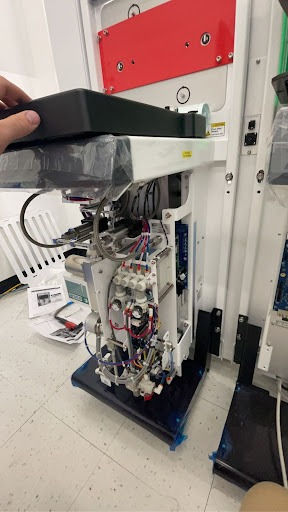
My last couple of weeks were spent as an intern for the Network Architect Christ Marrara. Walking into this job I did not know too much about what a network architect was. However, Chris showed me his everyday work and what it takes to be one. My job was to help him load and ship firewalls to other Brooks locations across the world. I sat beside him loading up each individual box and updating the software. I used my newly learned computer science skills to decipher the code and note the important information Chris needed to share with his coworkers. I also was assigned to search and find documents about the Radio Act Law in China and South Korea, which we needed to follow and fill out forms, as we were shipping firewalls to Singapore, Taiwan, and South Korea.
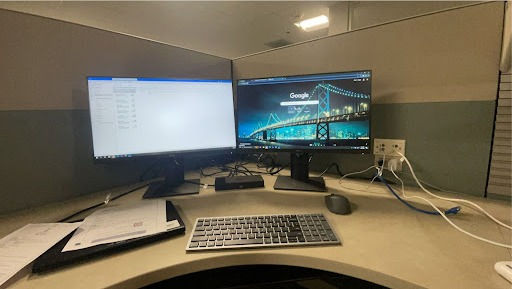
My experience at Brooks this summer has taught me so much about engineering, lab management, and what it’s like inside the semiconductor manufacturing business. I am grateful for having the opportunity to connect with many colleagues and other interns at the Chelmsford location who have made my internship experience so incredible. Thank you to everyone at Brooks Automation for working with me this summer to help me get the most out of my time at Brooks. I would also like to give a big thank you to Mr. Schlenker and Richie Mendes for making this internship possible and allowing me this special opportunity.
Comments